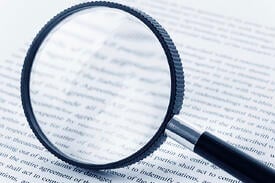
After you've documented the existing process, you can begin the work of targeting areas to be improved. Are there too many opportunities for errors? Is there a chance to implement automation? What are the bottlenecks that impede productivity? Are the right people working on the right parts of the process? Does the existing process support the company's overall strategy?
To ensure success, don't undertake this stage alone. Build a team that includes people from the original group that mapped out the existing process. Also, recruit staff from different levels of management to get different points of view. When appropriate, bring in vendors and outside consultants.
The team should question every step, however mundane. Investigate if new technology can add integrity or increase speed. Eliminate steps that don't add value. Nothing can be considered off-limits during this discussion phase.
When proposing changes, document the business reasons for doing so. Don't make changes for change sake. It's easier to support implementing modifications when you understand the reasons behind them. Also, this step provides a road map for future reviews and improvements.
Clearly state the goals of the process improvements. Establish objectives that can be accurately measured. Use the metrics determined earlier as a statement of the existing condition, or baseline. Set up a reporting format to review your progress. Be prepared to explain your successes and failures.
The power of "What if?"
Use the "What if?" methodology to uncover more improvements. For example, there are several "What if?" questions that could lead to improving a statement processing system. A short list would include:
- What if statements weren't printed, but offered in a digital format?
- What if print quality could be measured automatically during the process?
- What if printer/inserter speed could be increased by 10%? By 20%? By 30%?
- What if every piece could be tracked during production?
- What if color print was introduced to highlight important information?
+ Read More